How to improve the cutting accuracy of laser cutting machine?
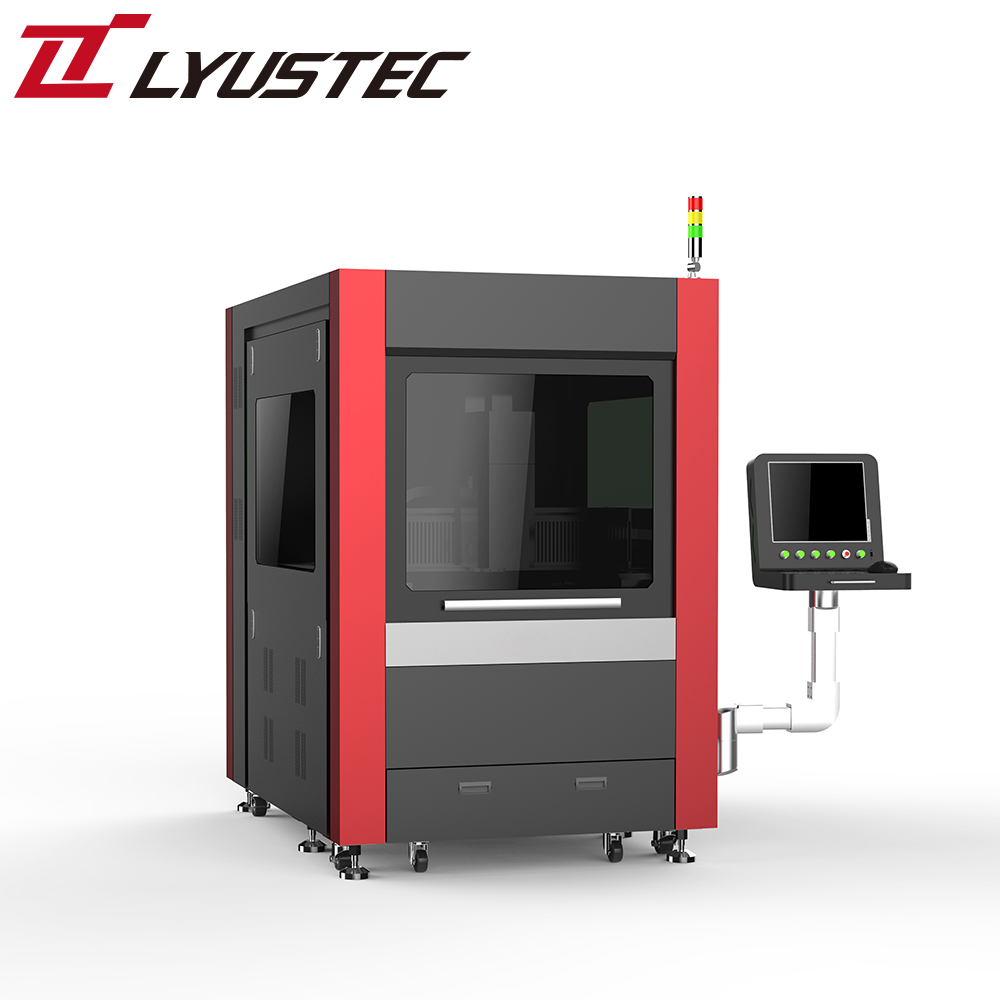
Analysis of measures to improve the cutting accuracy of laser cutting machines:
1. During the cutting process of the laser cutting machine, the beam is focused into a small focus by the lens of the cutting head, so that the focus can reach a high power density. The size of the focused spot of the laser beam: the smaller the focused spot of the laser beam, the higher the precision of laser cutting.
2. The positioning accuracy of the worktable determines the repeatability of the laser cutting process. The higher the accuracy of the worktable, the higher the cutting accuracy. The larger the workpiece thickness, the lower the accuracy and the larger the kerf. Since the laser beam is tapered, the kerf is also tapered. The workpiece material has a certain influence on the laser cutting accuracy. In the same case, the cutting accuracy of different materials is slightly different. Even for the same material, if the composition of the material is different, the cutting accuracy will also be different.
3. Focus position control technology to improve the cutting accuracy of laser cutting machine: the smaller the focal depth of the focusing lens, the smaller the diameter of the focus spot, so it is very important to control the position of the focus relative to the surface of the material to be cut.
4. Cutting and perforation technology to improve the cutting accuracy of laser cutting machine: any kind of thermal cutting technology, except for a few cases, which can start from the edge of the board, generally must pass a small hole on the board. Earlier, on the laser stamping compound machine, a punch was used to punch a hole first, and then a laser was used to start cutting from the small hole.
5. Nozzle design and airflow control technology to improve the cutting accuracy of laser cutting machine: When laser cutting steel, oxygen and focused laser beam are shot through the nozzle to the material to be cut, thereby forming an airflow beam. The basic requirements for the airflow are that the airflow entering the incision should be large and the speed should be high, so that enough oxidation can make the incision material fully perform the exothermic reaction; at the same time, there is enough momentum to blow the molten material out.
6. Laser cutting has no burrs, wrinkles and high precision, which is better than plasma cutting. For many electromechanical manufacturing industries, because the modern laser cutting system of microcomputer program can easily cut workpieces of different shapes and sizes (the workpiece drawings can also be modified), it is often preferred over punching and molding processes; although its processing speed It is slower than die punching, but it has no mold consumption, no need to repair the mold, and saves the time to replace the mold, thereby saving processing costs and reducing product costs, so it is more economical in general.
1. During the cutting process of the laser cutting machine, the beam is focused into a small focus by the lens of the cutting head, so that the focus can reach a high power density. The size of the focused spot of the laser beam: the smaller the focused spot of the laser beam, the higher the precision of laser cutting.
2. The positioning accuracy of the worktable determines the repeatability of the laser cutting process. The higher the accuracy of the worktable, the higher the cutting accuracy. The larger the workpiece thickness, the lower the accuracy and the larger the kerf. Since the laser beam is tapered, the kerf is also tapered. The workpiece material has a certain influence on the laser cutting accuracy. In the same case, the cutting accuracy of different materials is slightly different. Even for the same material, if the composition of the material is different, the cutting accuracy will also be different.
3. Focus position control technology to improve the cutting accuracy of laser cutting machine: the smaller the focal depth of the focusing lens, the smaller the diameter of the focus spot, so it is very important to control the position of the focus relative to the surface of the material to be cut.
4. Cutting and perforation technology to improve the cutting accuracy of laser cutting machine: any kind of thermal cutting technology, except for a few cases, which can start from the edge of the board, generally must pass a small hole on the board. Earlier, on the laser stamping compound machine, a punch was used to punch a hole first, and then a laser was used to start cutting from the small hole.
5. Nozzle design and airflow control technology to improve the cutting accuracy of laser cutting machine: When laser cutting steel, oxygen and focused laser beam are shot through the nozzle to the material to be cut, thereby forming an airflow beam. The basic requirements for the airflow are that the airflow entering the incision should be large and the speed should be high, so that enough oxidation can make the incision material fully perform the exothermic reaction; at the same time, there is enough momentum to blow the molten material out.
6. Laser cutting has no burrs, wrinkles and high precision, which is better than plasma cutting. For many electromechanical manufacturing industries, because the modern laser cutting system of microcomputer program can easily cut workpieces of different shapes and sizes (the workpiece drawings can also be modified), it is often preferred over punching and molding processes; although its processing speed It is slower than die punching, but it has no mold consumption, no need to repair the mold, and saves the time to replace the mold, thereby saving processing costs and reducing product costs, so it is more economical in general.